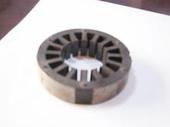
“模具钢材行业要学习贯彻党的十八大精神,转方式、优结构、提质量、增效益,实现创新驱动发展战略。”日前,国际模协秘书长罗百辉接受记者采访时表示,“转方式、优结构、提质量、增效益,创新驱动新发展”是模具钢材行业实现健康发展的最有效途径。
世界经济增长将处于一段较长时间的低迷期和结构大调整期,不稳定、不确定因素难以消除。罗百辉认为,依靠扩大出口拉动经济增长已经不可持续。国内经济正进入一个由高速增长向中速增长,由粗放式发展向集约化发展,由重视数量增长向更加重视发展质量和效益,更加均衡、协调、可持续发展的转折期。
“我国模具钢材企业面临两大机遇和两大挑战。”罗百辉指出两大机遇,一是今后十几年我国要基本实现工业化,信息化水平大幅提升,城镇化质量明显提高,农业现代化成效显著,以及国家大力推进战略性新兴产业给我国模具钢材企业创新发展带来的机遇。二是我国模具钢材企业近几年装备现代化和企业软实力的增强,为扩大国际市场特别是进军发展中国家市场,实施国际化经营带来了新机遇。模具特殊钢的特殊用途性质决定了要真正做强做大必须走专业化精品和国际化市场规模的发展之路。
目前,使用模具钢材的下游汽车、家电、医疗器械、LED、电力、机械等行业,增长速度明显放缓。但最近出台的《高端装备制造业“十二五”发展规划》明确了高端装备制造业发展的重点方向:航空装备、卫星及应用、轨道交通装备、海洋工程装备、智能制造装备等为模具钢材需求提供了新的亮点,对产品质量也提出了更高的要求。同时,党的十八大明确提出2020年要全面建成小康社会,国内生产总值和城乡居民人均收入要比2010年翻一番。这些都给模具钢材行业带来了新市场,给模具钢材企业提供了广阔的用武之地。
两大挑战,一是企业联合重组能否真正实现生产要素资源(人才、资金、先进设备)配置效率的提高,应对国际市场竞争的挑战。二是面对资源环境制约能否实行绿色制造,建设生态文明工厂的挑战。
罗百辉表示,目前我国模具钢材行业面临着区域分布不合理、产业集中度低、专业化分工程度低等问题。技术能力、管理能力、操作能力、市场开发能力不足已成为制约和影响模具钢材产业升级、技术进步的“瓶颈”。加之模具钢材企业自身投入能力有限,国家政策支持力度相对缺乏,我国模具钢材产业整体水平与国际先进水平之间存在很大的差距。
据了解,2012年我国模具钢材棒材生产线新投产6条,共新增产能630万吨,一半处于产能待释放状态,一半处于排产不满状态。由此可见。模具钢材行业已经出现产能集中投放的局面。对此,《全球模具配件大全》编委苏江武认为:“在这种情况下,即使模具钢材市场有所好转,企业也很难实现好的效益。”
数据显示,2012年模具钢材规模企业利润大幅度下滑,1月~9月份实现销售利润总额4.7亿元,比去年降低97%;利润率仅为0.87%。9月份,31家主导企业亏损13.3亿元,亏损企业24家,亏损面达77%,比8月份上升48个百分点,比去年9月份上升32个百分点。
由此可见,模具钢材行业的结构调整仍然任重而道远。
“目前,钢材需求的最低迷时期已经渡过,但并不意味着行业最困难的时期已经渡过。”深圳模具技术学会刘成洋副秘书长认为,2013年世界经济形势严峻,国内宏观经济增速放缓,房地产调控政策不会放松,行业新增产能有待释放等因素的综合作用,将使明年的形势更加复杂,不确定性因素增多。
“模具钢材行业整体供大于求的局面进一步加剧,2013年将比2012年更困难,过剩产能面临被迫淘汰。”刘成洋这样判断,“实际上,下游对优模具钢材需求出现了阶段性萎缩。”
模具钢材的主要下游行业是机械、汽车、铁路、船运等行业。1月~9月份,我国汽车产销分别为1413.12万辆和1409.23万辆,同比分别增长4.98%和3.37%。其中乘用车产销1136.71万辆和1126.96万辆,同比增长8.41%和6.94%,预计2012年全年产量1884万辆左右,同比增长2.3%。1月~9月份,我国机械行业总产值13.3万亿元,同比增长11.9%,预计2012年全年总产值17.7万亿元,同比增长4.9%。汽车产量和机械行业总产值虽有小幅度增长,但实际上,国内货车产销同比分别下降6.40%和8.26%,重型货车产销同比分别下降30.82%和30.91%。尽管用钢最多的重型货车降幅最大,由于近年来汽车用钢的高强度、轻量化和汽车产销的增长,2012年汽车模具用钢数量与去年相比仍处高位增长。
“面对两大机遇和两大挑战,企业必须从谋求长远可持续发展的高度与时俱进地调整发展战略,在企业管理、技术、产品和商业模式上创新,把发展的立足点由扩大产能规模转到提高发展质量和效益上来。”罗百辉指出,无论老的企业还是新的企业,都应该认识到再扩大产能的风险,把投资方向转到提质降耗、改善环保、发展循环经济和延伸产业价值链上来。
目前,我国模具钢材生产在数量上与国民经济发展大体适应,能生产大量高品质特殊钢,可以覆盖全部军工工程型号。但是,国内高端产品在品种质量上和数量上仍不能完全满足国内市场需要(合金钢比仅6.31%,不锈钢比仅1.55%),仍有相当数量的进口(每年进口合金钢约300万吨);部分高端产品不能满足国内行业发展及重大工程需求,核心部件材料不过关,飞机起落架、高速列车车轴、轴承等抗疲劳高强钢,核电站用耐高温、抗辐射不锈
耐热钢管,燃汽轮机、涡扇发动机的高温合金叶片等材料,目前还不能全部国产化。对此,罗百辉指出,当前,特别要把握好产品创新方向。一是服务传统用户创新升级的要求,开发钢材新品种新规格;二是跟踪战略性新兴产业发展,创新新品种和新材料,打造新的效益增长点。
目前我国大多数模具钢材企业均面临产业升级改造和产品结构调整的艰巨任务。模具钢材企业应结合当地的区域资源、市场资源、自身特点等,坚持淘汰落后、提高专业化分工程度、提高优势品种集中度的原则,为模具钢材产业合理布局、专业分工和产业集约奠定基础。
“作为企业自身,我们要做的就是进一步加快结构调整和产业升级步伐,加大资源优化重组和人才、科技创新队伍培养的力度,积极维护行业公平竞争秩序,积极寻求和构建上下游产业之间的战略联盟,抱团取暖、相互促进、荣辱与共,在促进产业集中度提升的同时,提高抵御市场风险能力和市场应变能力,真正把企业打造成符合时代发展要求,符合经济发展要求的经济实体,开拓出实现自身可持续发展的新路子。”苏江武如是说。